Projects Showcase
Selected highlights of our work
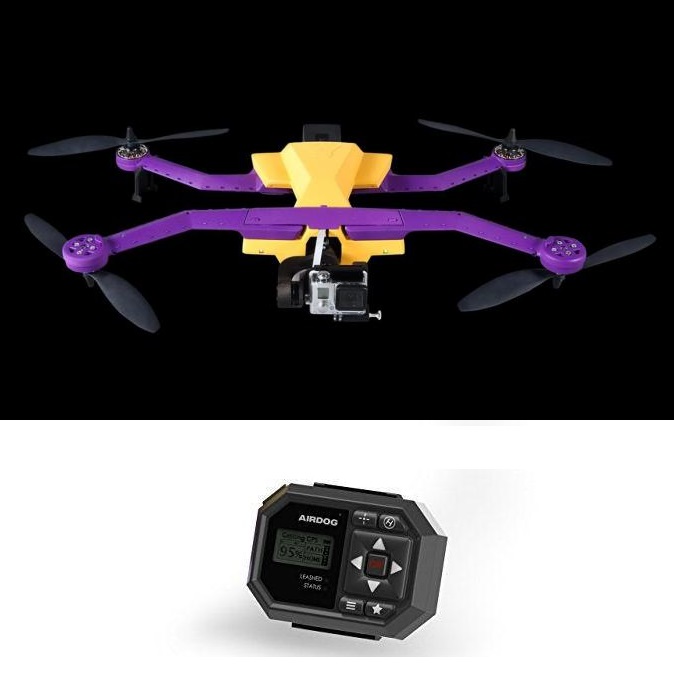
As part of the Airdog team, we designed and manufactured action sport drones. To bring the product to market, we addressed several key challenges:
- Durable electronics: Developed lightweight, cost-effective, and heavy-duty electronics capable of operating in harsh conditions, including impacts, vibrations, extreme temperatures, high altitudes, and exposure to saltwater and vapor.
- Sturdy enclosure: Engineered a robust yet lightweight and low-cost plastic drone enclosure optimized for mass production.
- Rugged remote control: Designed and implemented a handheld control device capable of withstanding drops, impacts, and submersion in saltwater, while integrating precision sensors such as GPS, pressure, and inertial measurement units.
- Reliable supply chain: Established and managed a supply chain by identifying and overseeing key component manufacturers in Mainland China and other regions.
- Scalable production: Successfully launched mass production in Latvia and scaled operations to Taiwan.\
As a result of these efforts, we created a product that was loved by customers, won a Kickstarter campaign, and received first prize at the CES exhibition.
Read less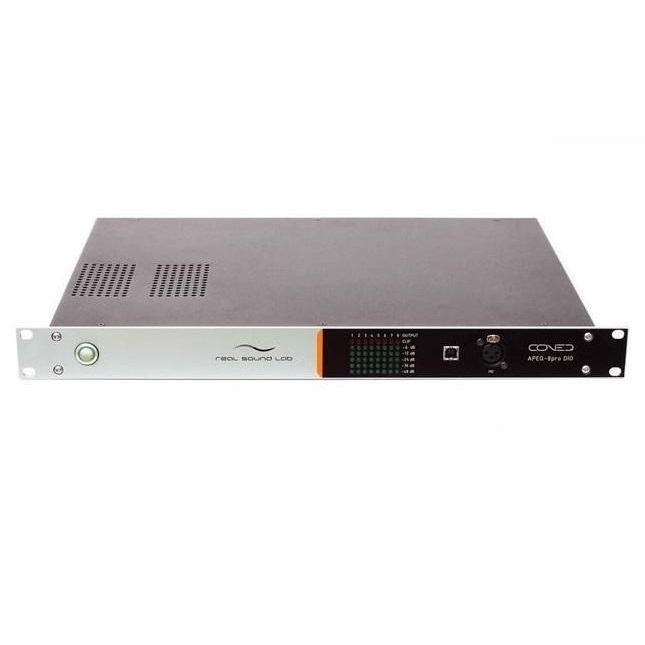
As part of the Real Sound Lab team, we designed and manufactured equipment for professional sound studios, concert halls, and high-end audio customers. To achieve the high performance required for these devices, we overcame several challenges:
- Low-noise, low-distortion analog circuits design.
- High-precision, low cost analog/digital (ADC and DAC) converters
- Low-latency, high performance FPGA based digital signal processor (DSP)
- Compact multi-channel design: Addressed challenges related to electromagnetic interference (EMI) and heat dissipation while maintaining a compact form factor.\
The resulting product was embraced by satisfied customers worldwide.
Read less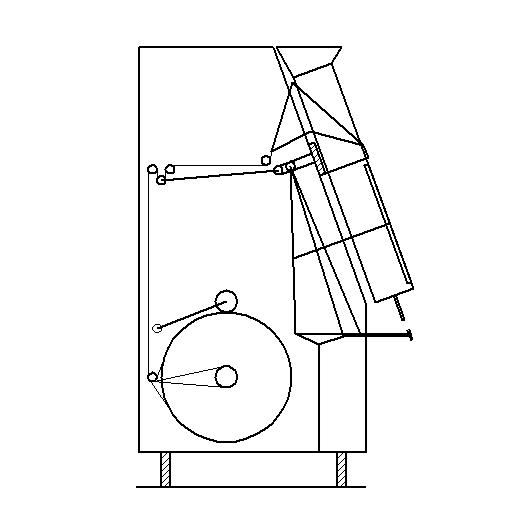
A customer acquired an old packaging machine designed to pack bulk products like salt into polyethylene or polypropylene bags. The machine originally featured a volume dosator and lacked any sensors, which significantly limited its efficiency. As part of this project, the machine was upgraded with a weight-based dosator, film damage sensors, precision temperature regulators for splicers, and an electronic control system. These upgrades considerably reduced the possibility of material loss or overspending, improved product quality, and enhanced overall equipment performance. As a result, the machine became capable of packaging more expensive products.
Read less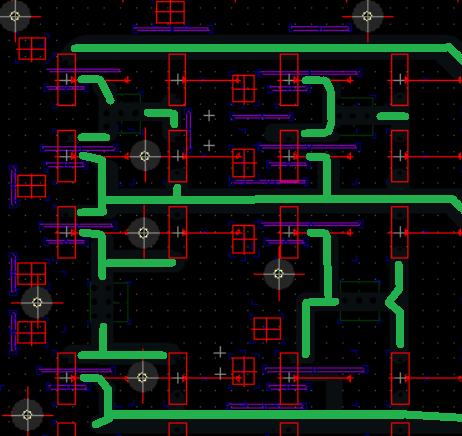
Unfortunately, many interesting and challenging projects cannot be shared here—they are still confidential and cannot be disclosed.
Read less